Expert Help for Effectively Starting a Microfactory
Why Choose In-House Production?
There are a variety of reasons to start a microfactory for your company, from wanting to re-shore your production to deciding to build your own manufacturing business from the ground up. One of the biggest reasons has to do with the cost of outsourcing production. Micromanufacturing your own products is often considerably less expensive in the long run, when compared to having a third-party manufacturer assemble products on your behalf. By starting your own microfactory, the money you spend will only be going toward your materials and labor, instead of subcontractors, additional fees, etc. Overall, you will save an average of 35-40% doing your own assembly.
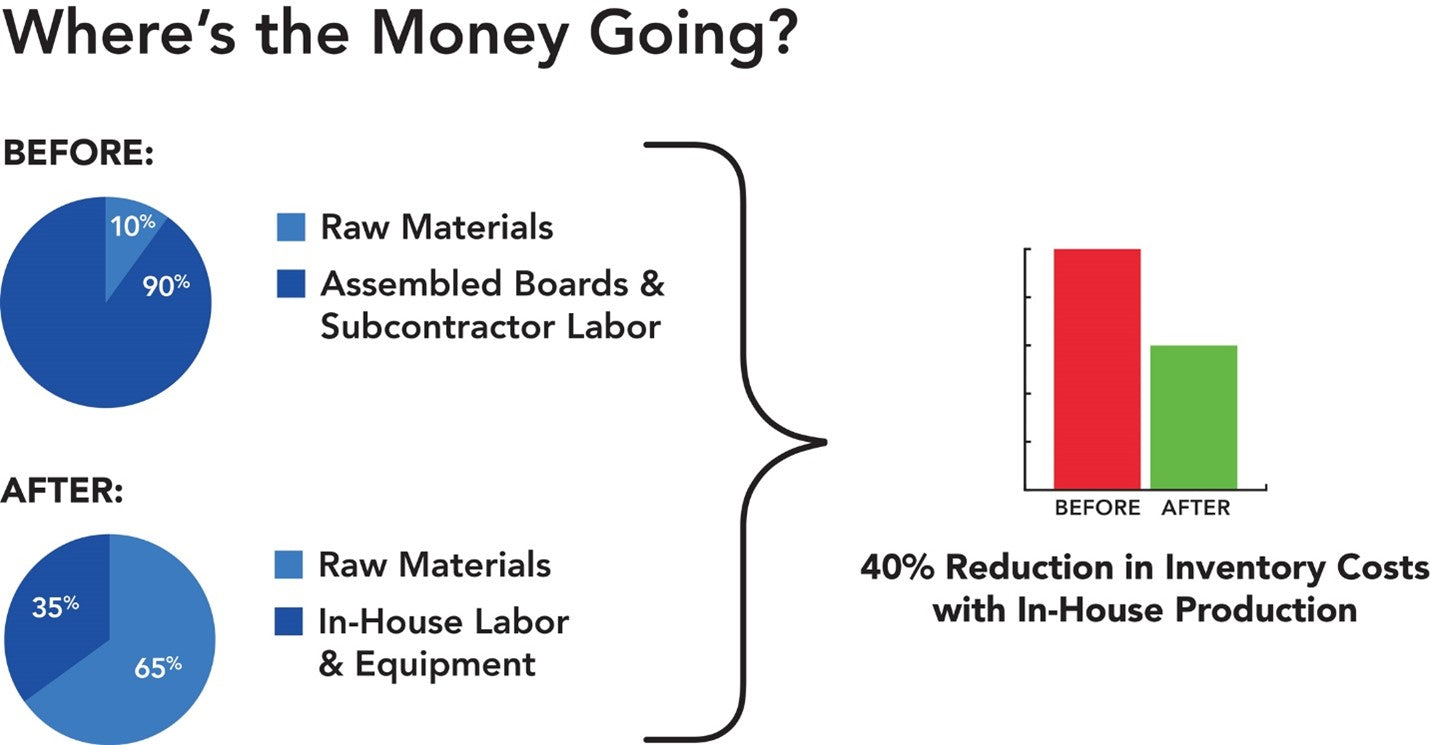
Plus, by bringing production in-house, you will no longer have to worry about not being a priority for that third-party contractor. Your company, your customers, will be the #1 priority for your micromanufacturing hub. This gives you the freedom to do small runs, produce on-demand, and so much more!
But how do you start your microfactory? The good news is you don’t have to do it alone. We will go over the main steps for getting started, so the process will be less daunting.
Step 1: Determine the Machines you Need

A main question you will need ask yourself is: What equipment will meet my company’s needs? While determining the best equipment, it can be really helpful to speak with a representative at your equipment supplier. These experts can field your concerns and expectations for micromanufacturing. At Manncorp, you will receive a full Bill of Materials analysis at no cost to you. Our team members will explain whether the equipment you are interested in will meet your company’s specifications. If some specs are not met, we will point this out and help you find the perfect machines for your unique needs.

It is important to find the equipment necessary to achieve your ideal setup and meet your company’s fulfillment requirements. A full consultation with one of our experts can help with that. Plus, we have on-staff technicians that can assist in setting up your equipment after it is delivered – whether you purchase a single machine or an entire manufacturing line. Beyond buying, we are here to help. Our team is on-call, on both coasts, to answer any questions you may have.
For a full list of questions to ask equipment suppliers during the buying process, all the things to look out for during the process, and some expert tips, check out our How-To Guide for Purchasing SMT Equipment. Ready to get started with choosing equipment? Check out some of our best preconfigured lines for microfactories in our overview on getting high-flexibility production for your microfactory or reach out to our team today.
Step 2: Customize Your Production Line Layout
Customizing Your Equipment Selection
If choosing one of our preconfigured equipment bundles doesn’t meet your needs, you can instead go the route of custom PCB assembly. You can cherry pick manual, mid-range, and automatic machines to suit your desired level of output. Mix and match to get your perfect combination. Just remember: You are only as fast as your slowest machine.

EQUIPMENT HIGHLIGHT
We have new feeders! Our new KFTA3D feeders will be available on MC machines from the MC400 and up. They are even better than our previous KFTA3 feeders, at the same price point. So, you get more without spending more. Our KFTA3D feeders have the following new enhancements:
- Component reel information is now stored/updated in the feeder.
- OLED displays allow for easy monitoring of the component consumption status.
- The feeder now has an internal battery, so data will always be available in both online (connected to machine) and offline (standalone) modes.
Customizing Your Equipment Layout
Once you have picked the perfect machine line-up for your company, it is time to talk about configurations. Many times – but not always – companies looking to run a microfactory are working within a compact space. Our team members are trained in designing an efficient layout of the equipment that works for your building. We also offer custom options, such as vertical ovens for saving space and conveyors that run right-to-left instead of left-to-right, so your equipment can be uniquely designed for your production setup.
Another aspect of designing your equipment layout is deciding on your organization method. In their microfactories blog, the company FormLabs breaks this organization down into 2 options: Per-Process or Per-Project.
- Per-process organization means organizing your space according to different stations that focus on different methods. The value of per-process planning is that it allows staff to run multiple orders simultaneously “since each order will occupy a different process at a different time”. The downside of this organization style is “if one order starts to back up or overwhelm the line, it’ll cause a ripple effect.”
- Per-project organization means separating orders into different lines. This organization style “increases flexibility and versatility, and it means you can use downtime on one line to handle overflow from another.” A drawback of per-project organization is that you need more machines. To run multiple versions of the same equipment, “you’ll need more resources upfront.” Because of the high up-front cost of this method, your production capacity could be limited by the number of lines your company can afford.
At Manncorp, our specialists can help you parse out the details. We will get you started down the right organizational path and determine the best configuration for your machinery, so you can maximize value and minimize equipment downtime.
Step 3: Have the Equipment Shipped & Installed
In addition to helping with the buying process and the layout design, Manncorp is also there through the shipping, delivery, and installation stages. An equipment supplier should do more than just supply equipment. We believe in customers receiving full support, for a lifetime.
This dedication to providing customers with all the help they need includes:
- Total transparency on how and when the equipment will be delivered.
- Guaranteed shipments from one of our two USA locations, from PA or CA.
- Clarity on when the shipment transfers to FOB delivery and any costs & risks associated.
- Easy integration of our machines for a seamless, connected assembly line.
- On-site installation help from one of our trained, in-house technicians.

One of the main benefits of choosing to move production in-house by starting a microfactory is the fast and easy set-up process. Installation of your microfactory can happen as quickly as one day.
For a traditional, sprawling factory, that timeline could look more like months or even years. The quick turnaround time means a quicker starting point for production, meaning a better chance of a quick break-even point through profit.
However, even with a microfactory, the deployment still requires a carefully planned delivery, detailed materials and instructions, and a knowledgeable technician for installation. For true success, you need a team of people putting care into each step, from their manufacturing facility to yours. To ensure the whole experience is a positive one, it is worth putting in the extra effort to find a provider who will make your microfactory delivery and installation their priority.
Step 4: Receive Staff Training on the Machines

Taking all the steps to get great equipment could be for nothing if you don’t have informed operators to run it. Make sure that your company has all the help possible at its disposal by choosing a supplier that offers training. A reliable equipment provider will have experts on-staff who understand the products well enough that they can offer in-depth explanations of how to run the machines, advice on maximizing the potential of the equipment for your specific needs—and provide troubleshooting if anything goes wrong.
With the purchase of any Manncorp equipment, we offer:
-
Easy Upgrades
We’ll deliver your equipment and help you install it. -
Set-Up Assistance
Our team can set up your new machine—or an entire equipment line. -
Hands-on Training
Receive custom training based on your company’s products and goals. -
Standard & Extended Warranties
Our worry-free options will ensure your investments are protected. -
Lifelong Support (24/7)
Get questions answered or help solving problems – any day, any time. -
Diagnostics & Repairs
Equipment issues will be diagnosed quickly and resolved simply.
Get Started
Learn more about what Manncorp can do for you. Or, if you are ready to start discussing the steps for starting your own microfactory, reach out! Our team members are happy to discuss options with you, provide you with a free BOM analysis, and more. Call 215-830-1200 on the East Coast or 858-490-6266 on the West Coast—or send an email to sales@manncorp.com.
