
Advanced Features Made Standard
The CR4000C reflow oven matches the capabilities of larger ovens feature-for-feature while saving you in space, energy usage, and upfront costs. Unlike other compact ovens, which use Infra-Red as their heating method, the CR4000C uses true forced-convection heating. The result is unmatched thermal performance; its edge-to-edge uniformity is ±2°C.
The conveyor system features a pin/edge conveyor over stainless steel mesh that can handle assemblies up to 16" (400 mm) wide. This combination conveyor provides you with maximum board handling flexibility and double-sided board processing capability. The pin conveyor's automatic oiler is software-driven for optimal preventative maintenance. Additionally, motorized width-adjustment is offered as a possible option and is based on specific reflow parameter settings that you can customize.

Real-Time Temperature Profiling and Profile Prediction
The CR4000C's onboard computer comes pre-loaded with Windows-based, password-protected* software. The partnered KIC Auto Focus profile prediction software permits on-screen profiling, with thermal data from up to 3 separate thermocouple inputs can be charted on-screen in real time. By inputting the board's physical characteristics (length, width, and weight), as well as your solder paste type, the software will suggest settings for belt speed and heating zones, producing a perfect profile before the first board is even run. This can be an incredible time saver when compared to traditional profiling methods.
*Password protection keeps basic operator functions separate from critical parameter settings that should only be altered by supervisors or production managers.
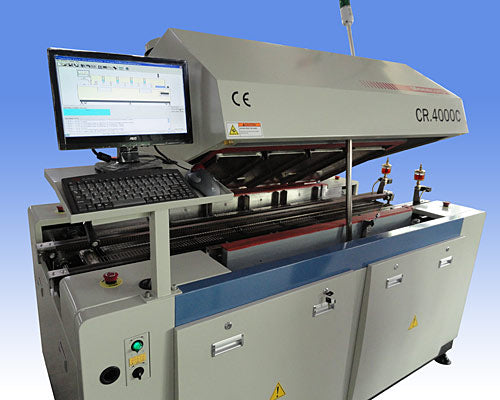
Low Energy Consumption and Reliable Results
This energy-efficient, environmentally friendly 6 ½ ft. unit consumes only 5-8 kW of electricity, even when ramped up to lead-free soldering temperatures of 300°C. For temperature profiling and thermal management, 3 thermocouple inputs come standard on the unit.
The four, independently controlled, forced-hot-air convection zones of the CR4000C's high-mass heating panels, and its two bottom-side convection zones (which span a total heating length of 52" [1320 mm]), will provide you with reliable, easily replicated results.
Timed startup and shutdown functions allow you to coordinate warm-up and cooldown times with production breaks and transitions between three separate shifts in each 24-hour period, promoting production preparedness and energy savings.
CR4000C Specifications | |
---|---|
Lead Free | Yes |
Nitrogen Available | No |
Mesh Belt Width | 20" (500 mm) |
Pin Conveyor | 16" Max. (400 mm) Hand Crank. Power Adjust (optional) |
Conveyor Speed (per min) | 7.8-35.4" (200-900 mm) |
SMEMA Compatible | Optional |
Component Max. Height | 30 mm upper, 25 mm lower |
Forced Convection | Yes |
Number of Heating Zones | 4 Independently Controlled Topside Convection Zones 2 Lower Convection Zones Controlled by Topside 1 Cooling Zone |
Heated Tunnel Length | 52" (1320 mm) |
Delta T | ±2° C |
PID* | Yes |
Max Temperature | 300° C |
Ramp Time (from cold start) | ~45 min |
Flux Management System | No |
Control | PC |
On-Board Profiling | Yes |
Dimensions | 2000 mm L x 1200 mm W x 1450 mm H (79" L x 47.2" W x 57" H) |
Weight | Approx. 950 kg (2095 lbs.) |
Power | 220 V, 3-Phase, 60 A, 15KW |
Required Active Exhaust | 400CFM per port |
# of Exhaust Vents | 2 |
Battery Backup | UPS Uninterruptible Power Supply for Conveyor & PC |
Hood Opening Mechanism | Automatic Raise and Lower |
*(Proportional-Integral-Differential)
How 'Auto Focus Power' Profile Prediction Works:

1. Select Your Solder Paste Formula and Process Window
The KIC Auto-Focus Power software includes a database of over 1000 different solder paste formulas from dozens of different solder paste manufacturers. Each database entry includes the manufacturer's recommended solder profile for that specific solder paste formula and identifies critical specifications (i.e. maximum ramp rate, maximum cooling rate, temperatures for preheat, soak, reflow, and peak, allowable times above those temperatures, etc., with upper and lower limits for each) that define the process window. After selecting the solder paste, users can either use the profile as is or can modify the specifications to create a process window that meets their own unique criteria.

2. Link Your Product to the Process Window
Once the Process Window is selected (defined), the next step in using Auto-Focus is selecting the product to be soldered (or assigning a name if the product has not yet been defined). This step, in effect, links the product to the selected process window. It also links the process window and the product to the CR Series Oven data in the database. The oven data has been produced by KIC's characterization of the unique thermal properties of specific CR Series oven models as they relate to varying product sizes and processes.

3. Define the Product's Physical Characteristics
The user now enters the average length, average width, and total weight of the product.

4. Obtain and Confirm the Oven Settings
Auto-Focus now scans the built-in database for zone temperature/belt speed settings that produce a thermal profile that best fits within the process window when soldering a similarly sized product. By comparing that profile to the desired process window, Auto-Focus is able to estimate the PWI™ (Process Window Index); a single value that will give the user an indication of how far "within spec" the actual profile will be when using the recommended oven settings. If the PWI value is acceptable, the user can then obtain the exact temperature settings for each zone along with the belt speed.