Smart, Compact, Inline
Sherlock 500L integrates cleanly with your existing production line to provide complete defect coverage before and/or after reflow or after wave soldering. Powerful algorithm-based software detects defects and helps to improve your process. Programming can optionally be done at an offline station to prevent disruption of production.
Post-inspection, Sherlock 500L sends the appropriate signal to downstream equipment, allowing passed PCBs to continue down the line or be unloaded to a rack. If it is rejected, it can be stopped at an inspection conveyor or unloaded to a separate rack marked for rework/repair.

Easy to Program and Operate
All programming and operation is done through the Sherlock-500L's intuitive touch-screen interface. Automatic pick & place and CAD data conversion and a pre-defined, customizable parts library not only speed up programming but also eliminate the need for skilled AOI personnel.
Unlike the libraries included with many other systems, the Sherlock 500L library contains comprehensive inspection data for each part, including image processing settings, lighting conditions, areas to be checked, and more. Custom parts can be quickly created from any pre-defined part.
The software is designed for ease of use, with an instantly intuitive interface. For added guidance, "Navigation Mode" can walk the operator through tasks step-by-step, and online help is always just a click away.
For optimum speed and traceability, the Sherlock 500L's camera reads both 2D and linear barcodes, eliminating the need for a separate barcode scanner. It also supports character recognition, enabling the system to process and compare component labels.
Additional features include intuitive zoom functionality for inspecting defects and quick statistics to highlight defective parts, providing operators with an efficient way to manage quality control.

High Defect Coverage
Sherlock 500L uses a high-resolution, 4-megapixel CMOS camera, a large-aperture telecentric lens, and two lighting systems to achieve fast, accurate inspection of both solder quality and components at a scanning rate of 7,000 mm2/sec.
The RGB+W LED lighting system inspects solder fillets for volume and shape. The three-tier white lighting system inspects component placement and positioning, with reflection and shadow controls to ensure low false calls and low false accepts.
The standard lens inspects parts down to 0201, or the Sherlock 500L can be fitted with a high-magnification lens to inspect parts down to 01005. Both of these telecentric lenses eliminate perspective errors, reduce distortion toward the edges of the field of vision, and provide uniform image plane illumination.
There is no need for the expense of high-megapixel cameras or multiple side-angle cameras with this system. It has been designed to provide accurate, reliable inspection results with the lowest complexity of programming and at a cost that's within reach of small and medium manufacturers.

Quality Components Throughout
During inspection, the camera moves, rather than the PCB. This ensures the clearest possible images and fastest inspection speeds. The camera motion system is X-Y bi-axial belt-driven with 50 µm positional accuracy.
The board transport system automatically adjusts to the size set in the program. Sherlock 500L comes standard with a pneumatic PCB stopper and vacuum clamp. It can optionally be purchased with a motor to eliminate the need for a compressed air source.
Operation is smooth and quiet, thanks to the machine's sturdy, vibration-damping construction.
All components are high quality, Japanese-made.
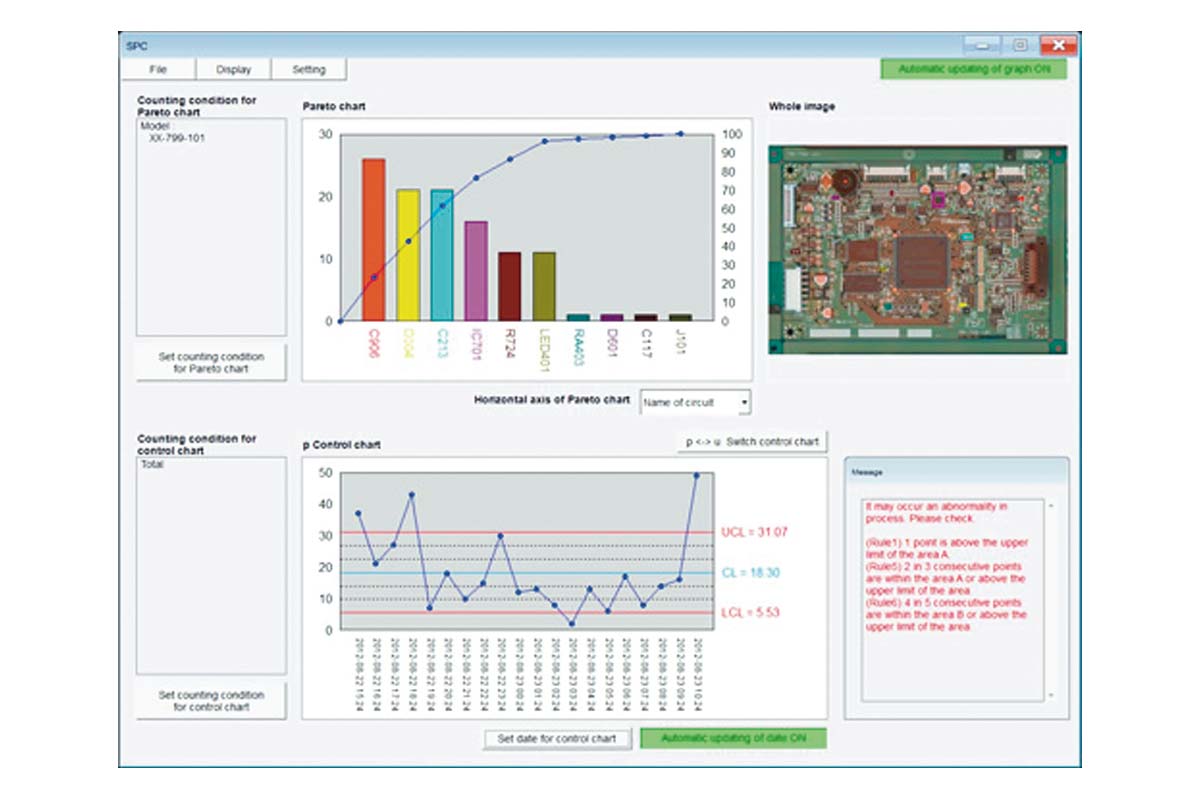
Keep Control of Your Process
Do more than detect bad PCBs. Improve your whole process with the addition of statistical process control (SPC) software. This software, installed on a separate computer from the Sherlock 500L, allows you to detect process abnormalities early, view trends over time, and discover where your problem areas are.

Trace and Repair
Repair station software designed to work with the Sherlock 500L simplifies rework by providing details at the repair station on each rejected board. Repair station personnel can access an image of the rejected part, with its location, name and details of inspection. With the connection of a bar-code reader, board data can be brought up on screen with a quick scan of the PCB's label.
History of inspection and repairs can be search by serial number. When linked with the SPC software, repair data can be tallied, providing complete traceability.
Defect Coverage
Sherlock 500L's scanning speed is independent of the number of components on the board: even densely populated boards are scanned at rates of 7,000 mm2/second. Fast cycle times keep the system from bottlenecking production—a 7.3" x 5.1" (185 mm x 130 mm) PCB with 253 parts can be processed in 10 seconds, including load and unload time.
Sherlock 500L is capable of detecting, with high accuracy:
- Solder joint defects
- Presence of solder
- Insufficient solder
- Excessive solder
- Opens
- Cold solder
- Solder balling
- Bridging
- Poor soldering
- Lifting
- Fillet coverage (THT)
- Wetting (THT)
- Partial and full lack of solder (THT)
- Blowholes (THT)
- Component defects
- Missing or extra components
- Wrong components
- Shifting
- Tombstones
- Reverse polarity
- Damaged parts
- Bent IC leads
- Pin presence (THT)
- Bent pins (THT)

One-Year Warranty + Remote Service Support
To protect your investment, the Sherlock 500L comes with a 1-year parts warranty and access to telephone and email technical support. Manncorp technicians are employees, not contractors, with years of experience at all levels of circuit board assembly.
Remote service support software and a network adapter comes with every Sherlock 500 series machine, allowing Manncorp technicians to troubleshoot remotely over the Internet.
Sherlock 500L Specifications | |
---|---|
Component Coverage | Down to 0201 (01005 available) |
Minimum PCB Size | 2" x 2" (50 mm x 50 mm) |
Maximum PCB Size | 20" x 18.1" (510 mm x 460 mm) |
Topside Clearance | 1.18" (30 mm) with standard lens, 0.98" (25 mm) with high magnification (including PCB thickness) |
Bottomside Clearance | 1.18" (30 mm) |
Lighting System | Circular LED lighting RGB+W and warm-white illumination in 3-ring arrays |
Camera | 4-megapixel color camera with 2/3" CMOS sensor with Camera Link for high-speed data transmission and telecentric lens |
Resolution | 20 µm standard lens 14 µm high-magnification lens |
Depth of Field | 0.39" (10 mm) standard lens 0.24" (6 mm) high-magnification lens |
Field of View | 1.61" x 0.87" (41 mm x 22 mm) standard lens 1.14" x 0.59" (29 mm x 15 mm) high-magnification lens |
Inspection Speed | 7,000 mm2/sec |
Motion Control | Bi-axial (X-Y) belt-driven |
Repeat Position Accuracy | 50 µm |
Control Resolution | 10 µm/pulse |
Programming | Automatic CAD conversion, pre-defined customizable component library, touch-screen-based teaching |
Offline Programming | Available |
Repair Station Software | Available |
SPC Software | Available |
Computer Control | Core 4 Xeon with 8 GB RAM, Windows® 10 OS |
Power Requirements | AC100V to 240V single-phase |
Air Supply | 0.5 Mpa, 5 l/min(ANR) |
Environmental Requirements | Operation: 10 to 35° C/30-80% non-condensing RH Storage: -10 to 60° C/30-80% non-condensing RH |
Weight | 337 lbs (153 kg) just the unit 386 lbs (175 kg) including PC |
Dimensions (L x W x H) | 36" x 36.5" x 53" (920 x 927 x 1356 mm) (Alert light adds 11" (280 mm) in height) |
Warranty | 1 Year |
Remote service & support | Included |